Assessing Why Automated Sterile Tube Welder Technology is the Most Reliable Option for Cell Therapy Manufacturing
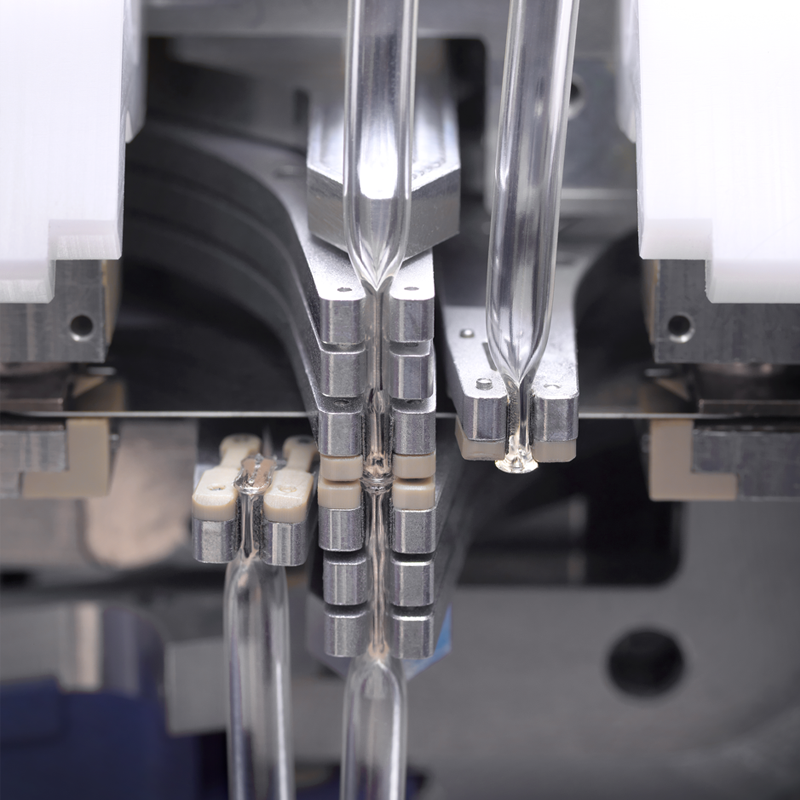
Successfully industrialising and scaling cell therapies with robotic automation requires reliable aseptic connections into and between all unit operations. Every fluid transfer connection presents a potential gateway for contamination and ensuring absolute sterility at these critical interfaces, whether modular or integrated, is non-negotiable. This post delves into a cornerstone of our Constellation platform: our meticulously chosen method for making automated sterile connections – sterile tube welder technology.
When designing Constellation, we explored various options for ensuring reliable aseptic connections between different processing steps. Ultimately, we selected sterile tube welder technology. Why? Because it offers significant advantages: it’s a process trusted by regulators, capable of achieving the high reliability needed to prevent contamination, and compatible with existing cell therapy consumables.
The Critical Role of the Sterile Connection
In cell therapy, maintaining sterility is paramount. The connection points between different bags, bioreactors, and processing equipment are potential points of failure where microbial contamination could occur. Implementing a closed process, and the associated requirements for sterile connection, is critical to enabling manufacturing to carry out the process in low grade cleanrooms (Grades C/D), significantly reducing facility and running costs.
But how sterile is sterile enough? Maintaining product sterility is the most critical function of any connection step within the overall Contamination Control Strategy (CCS) for cell therapy manufacturing. The effectiveness of this strategy is often validated through Aseptic Process Simulations (APS), sometimes known as media fills. In a typical APS, the aim is to demonstrate an extremely low rate of contamination events, ideally less than 0.1%, across the entire simulated process. Achieving this stringent target requires each connection, along with every other aseptic manipulation, to be performed with exceptionally high reliability to prevent any microbial ingress, including bacteria, spores, and pyrogens.
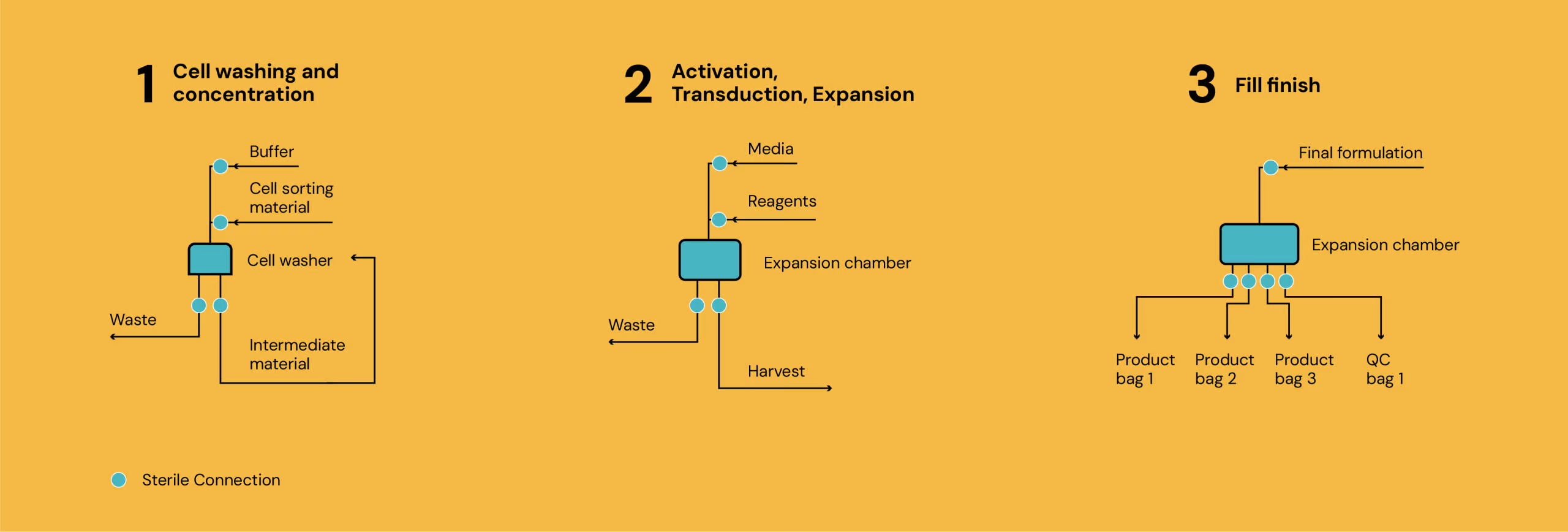
Illustration of sterile connections in cell therapy process
Evaluating the Options
Feature | Sterile Tube Welding | Single-Use Aseptic Connectors | Reusable Aseptic Connectors | Needle-Free Connectors |
---|---|---|---|---|
Sterility Assurance | High | High | High | Lower (Septum surface risk)* |
Connection Reusable | Yes (though tube length can be lost) | No | Yes | Yes |
Disconnection | Requires Tube Sealer | Requires Tube Sealer | Integrated / Requires Tube Sealer | Integrated |
Recoverable (on Failure) | Yes (Cut & re-weld nearby possible) | No | No | No |
Consumable Cost | Low (Blade); Uses standard tubing | Medium (Per connector unit) | High (Per connector unit) | Medium (Per connector unit) |
Consumable Complexity | Low (Uses existing standard tubing) | Medium (Requires pre-attachment) | High (Requires pre-attachment) | Medium (Requires specific ports) |
Automation Complexity | High (Precise mechanics, heating) | Medium (Robotic handling/actuation) | Medium (Robotic handling/actuation) | Medium (Handling & Disinfection)* |
Typical Environment | Grade C/D (Enables closed process) | Grade C/D (Enables closed connection) | Grade C/D (Enables closed connection) | Grade A (Requires aseptic technique) |
Regulatory Acceptance | High (Well-established) | High (Established for SU Bioprocess) | Medium (Limited use in CGT Mfg) | Low (Not suitable for Mfg outside A) |
*Notes: Needle-free connector sterility assurance heavily relies on meticulous aseptic technique during use (standard disinfection may be insufficient for spores) and is typically restricted to Grade A environments for manufacturing steps. Automation complexity includes necessary disinfection protocols.
We considered several methods for making sterile connections:
1. Sterile Tube Welding: Creates a permanent, closed connection by melting and fusing two pieces of thermoplastic tubing. It is recoverable if a weld fails (you can often cut and re-weld nearby) and uses standard, low-cost tubing. However, it requires complex automation and requires the handling of flexible tubing.
2. Single-Use Aseptic Connectors: Pre-sterilised, disposable connectors that click together. They are quick and simple to connect, and can bridge consumables with dissimilar tube types. They are also familiar to regulators. However, they require specific connectors to be pre-attached to all consumables, which isn’t standard, and are not reusable so manifolds can become bulky if many connections are needed.
3. Reusable Aseptic Connectors: Allow for multiple connections and disconnections. In many ways these are ideal in principle, however, in practice these are mechanically complex, costly, and all existing such connectors are too large and not suitable for typical cell therapy consumable sizes, hence they are not widely used in cell therapy currently. They also still require specific connectors to be added to consumables.
4. Needle-Free Connectors: Common in hospital IV settings, but generally not considered sufficiently sterile for cell therapy manufacturing particular for multi-use connections. While used in hospitals for IVs, this relies on the patient having an active immune system to combat minor contaminants – a luxury absent in ex vivo cell processing, and hence these connectors are typically only used in a Grade A (already sterile) environment. Standard disinfection (like IPA wipes) is not sufficient sterilization to remove spores and other contaminants from the septum face.
Why we chose Automated Sterile Tube Welding
Constellation carrying out a Sterile Weld
Sterile welding requires more automation to be developed than some connector-based methods, given its requirements for precise motion control, heating elements, and cutting mechanisms. So why choose it? Despite the automation challenge, sterile welding emerged as the superior choice for integration into a closed, automated system like Constellation for several key reasons:
Regulatory Acceptance: It’s a well-understood and trusted method – 10,000s of sterile welds are performed in commercially approved cell therapy processes each year.
High Reliability: When automated correctly, it can achieve the extremely high success rates needed to guarantee a low rate of contamination. Furthermore, the weld can be inspected to check it has been performed successfully.
Consumable Compatibility: It works directly with the standard, low-cost thermoplastic tubing already used on most existing cell therapy bags and kits, avoiding the need to modify these consumables with connectors.
Recoverability: If an error occurs during the automated welding process, the system can potentially seal the tubes and allow for a re-weld attempt nearby.
Designing and testing a Robotic Sterile Tube Welder
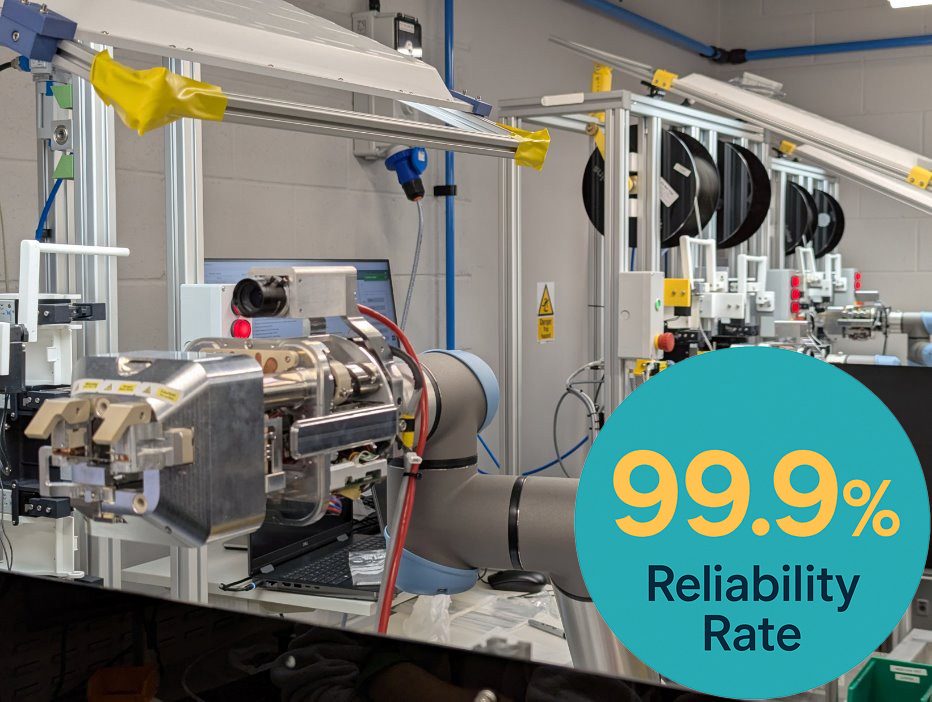
Robotic Sterile Tube Welder Testing at Cellular Origins
The challenge, therefore, wasn’t the principle of welding, but mastering its automation. Integrating sterile welding into a robotic platform required significant engineering ingenuity. We had to design a sterile tube welder not only lightweight enough for robotic integration but also capable of autonomously gripping and precisely engaging the tubing. We engineered a custom, integrated robotic end-effector that performs the entire welding sequence, including automated post-weld steps like ‘unpinching’ to eliminate manual intervention.
Furthermore, closed-loop control algorithms continuously monitor critical parameters, such as blade temperature, ensuring weld consistency and enabling real-time process tracking. A key advantage of automation is comprehensive data capture. For every weld performed, critical parameters such as blade temperature profiles, heating duration, fusion time, and motor currents are automatically logged, creating a detailed batch record and facilitating process analysis and control.
Given that reliability is crucial, we embarked on an extensive sterility testing program. Using dedicated test rigs, we performed over 3000 automated sterile tube welds under various conditions to rigorously assess consistency and reliability. Each weld underwent stringent integrity testing including pressure decay testing to verify leak tightness, supplemented by visual inspection.
The results confirmed the robustness of our approach: Constellation’s automated sterile welding achieved an outstanding 99.9% reliability rate (with 95% confidence), reinforcing its suitability for GMP-compliant manufacturing. Automating the process also enables rapid testing cycles to continuously verify performance.
The Future is Automated and Reliable
Automated sterile welding, integrated within a modular platform like Constellation, addresses a critical bottleneck in cell therapy manufacturing. By leveraging standard tubing and providing high reliability through automation, it simplifies workflows and supply chains without compromising the critical need for sterility. This paves the way for more efficient, scalable, and accessible cell therapies.
Looking ahead: Automating closed sterile connections is a key enabler for fully automated robotic factories. Next time, we’ll explore the evolving landscape of robotic automation, comparing and contrast different , from self-contained “robotics in a pod” solutions to the flexibility of mobile robots and the established utility of static robotic workcells.
Constellation
Constellation is a fully automated, mobile robotic platform enabling seamless scale-up from clinical to commercial cell therapy manufacturing. It integrates modular, proven third-party instruments and automates all critical GMP steps, with a unified digital layer for real-time monitoring and full traceability. By scaling only when needed, it reduces regulatory risk and labour reliance. We also support facility design and strategy to help developers confidently industrialise manufacturing.
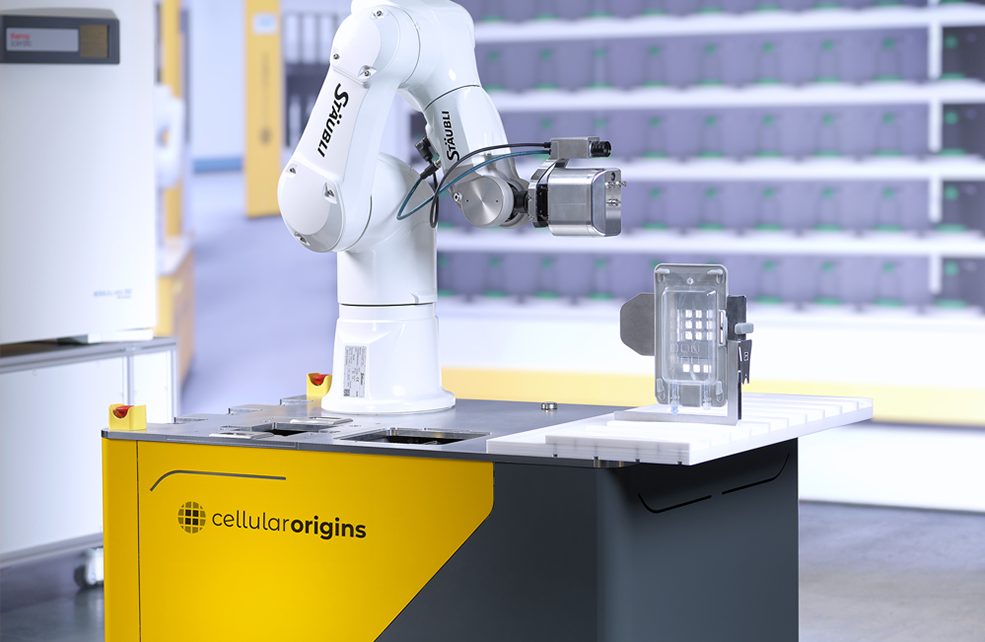